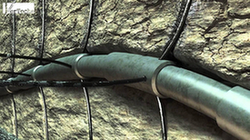
Oil and gas exploration is a dynamic industry, and new innovations are constantly being developed to enhance operational effectiveness, financial viability, and environmental sustainability. In recent years, “Wellbore Strengthening” and “Fluid Monitoring Systems,” two such innovations, have become well-known for their revolutionary effects on drilling operations. When these technologies are combined, a synergy is created that improves well integrity, lessens drilling difficulties, and guarantees optimal reservoir performance.
In a process known as wellbore strengthening, all fractures and vugs must be perfectly sealed using the right fracture seal materials in order to achieve quick, safe, and affordable drilling operations through formations containing natural fractures, or vugs. Through this strengthening process, the treated formation’s overall tensile strength may be increased to a level that is comparable to the inherent tensile strength of unfractured rock.
The suitability of fracture seal materials for applications involving the strengthening of wellbores in various formations has been tested in a number of studies. However, the strengthening procedure’s ability to restore the tensile strength and, consequently, the fracturing pressure of the naturally fractured formation is not adequately explained by any straightforward or reliable theory.
Understanding Wellbore Strengthening
A variety of methods used to reinforce the wellbore wall are referred to as wellbore strengthening. This reduces the risk of drilling fluids leaking into the formation. As fluid loss can result in formation damage, instability, and compromised well integrity, this is a serious concern during drilling operations. The traditional method frequently entails bridging and sealing formation fractures with lost circulation materials (LCMs) injected into the drilling mud. However, this approach may be ineffective and harmful to the environment.
Advanced strengthening methods take a comprehensive approach, combining LCMs, fiber materials, and custom drilling mud formulations. These techniques improve the mechanical strength of the wellbore, preventing well collapse and increasing overall stability, in addition to effectively sealing fractures. This is especially useful in geological formations that are difficult to understand and have a high prevalence of naturally occurring fractures.
Fluid Monitoring Systems: Navigating Drilling Fluid Dynamics
Real-time insights into the behaviour and condition of drilling fluid are provided by fluid monitoring systems, which have changed the game in drilling operations. To give operators a thorough understanding of fluid properties, flow rates, pressure differentials, and contamination levels, these systems make use of sensors, data analytics, and visualization tools. Drilling teams can reduce downtime and increase drilling efficiency by carefully monitoring these parameters. By doing so, they can identify problems early on, optimize drilling mud composition, and make informed decisions.
Merging Wellbore Strengthening and Fluid Monitoring
Although fluid monitoring and strengthening systems are powerful tools on their own, their full potential is only realized when they are combined into a single, cohesive strategy. The mutually beneficial relationship between these technologies fosters continuous drilling process improvement.
Utilizing strengthening techniques reduces fluid loss when drilling in fracture-prone formations. In addition, fluid monitoring systems keep a close eye on the behaviour of the drilling fluid to make sure that the selected strengthening strategy is still working in real-time. The system notifies the operators if it discovers any deviations, allowing them to swiftly modify the drilling mud formulation.
In contrast, strengthening monitoring systems helps provide accurate baseline data. Monitoring systems may pick up anomalies that might otherwise be misinterpreted as variations in drilling fluid behaviour when the integrity of the wellbore is threatened by fluid loss. A strong wellbore improves the accuracy of the fluid monitoring data, increasing the drilling operations’ overall effectiveness.
Advantages of the Merged Approach: Efficiency, Cost Savings, and Sustainability
A number of benefits that go beyond better drilling operations are brought about by the integration of wellbore strengthening and fluid monitoring systems.
- Operational Efficiency: By preventing fluid loss and maintaining consistent drilling fluid properties, the merged approach minimizes downtime caused by well instability and fluid-related complications.
- Cost Savings: Due to the ability to conserve drilling fluids and related materials, the reduction in fluid losses results in significant cost savings. Furthermore, proactive problem detection through fluid monitoring avoids expensive equipment failures.
- Environmental Sustainability: Environmental impact is lessened as a result of decreased fluid losses and improved drilling fluid composition. Less drilling fluid is lost into the formation; reducing the chance that groundwater will become contaminated.
- Enhanced Safety: A strengthened wellbore improves safety by lowering the possibility of well collapse, which can be a risk during drilling operations.
- Reservoir Performance: The performance and recovery rates of a reservoir can be enhanced by stabilizing the wellbore and modifying the composition of the drilling fluid.
Conclusion:
In conclusion, the integration of fluid monitoring and wellbore strengthening systems embodies the creative spirit of the oil and gas sector. Drilling operations are made more dependable, effective, and sustainable by combining these technologies. The integrated strategy fosters a proactive mind-set when dealing with drilling challenges in addition to improving well integrity. Together, these technologies will undoubtedly remain at the cutting edge of developments as the industry develops, changing how we extract and use essential energy resources. Vertechs is a leading provider of top-notch services and products for wellbore processes. If you have any requirements for services and products for your wellbore drilling operations, then we are always available to serve you.